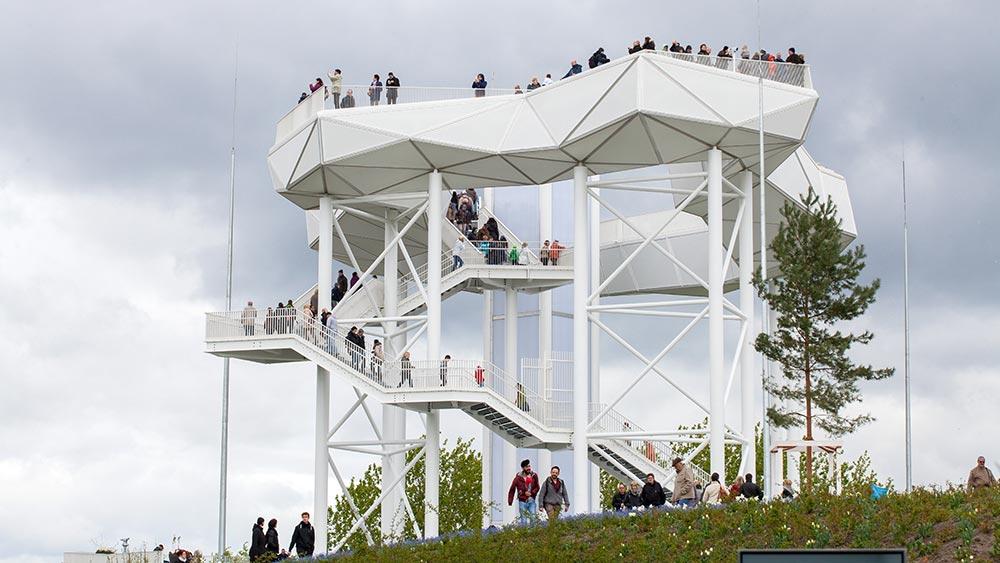
120 meters above sea level, the Wolkenhain viewing platform is enthroned in the middle of Berlin's Kienberg. From the landmark of the 2017 International Garden Exhibition, visitors have a view of Berlin's city center and beyond. At night, the upper part of the construction, which resembles a cloud, is illuminated in different colors.
The contractor, Vollack Hallen- und Stahlbau GmbH & Co. KG, relied entirely on Building Information Modeling (BIM) for this challenging structure. With the help of model-based planning and execution, the company was able to implement the complex concept of the steel structure.
It all starts with the 3D model
For Vollack Hallen- und Stahlbau, the 3D model is always the first step in the BIM process. In the Wolkenhain project, the architect responsible had already created an initial 3D model using Rhino software. Vollack was now given the challenging task of realizing the design in collaboration with the structural engineer. The steel fabricator with branches in Karlsruhe and Mihla in Thuringia was responsible for the planning, production and execution of the structure.
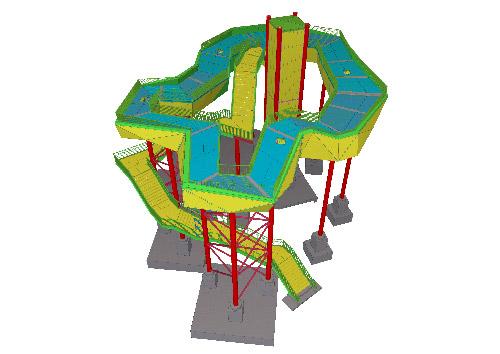
The construction consists of 160 solid spherical nodes with up to nine connections that hold the struts of the viewing platform together. The cloud, which consists of a translucent membrane, rests on slender, irregularly arranged steel supports. These are modeled on the trunks of a grove of trees. Vollack used the BIM software Tekla Structures from Trimble to plan the entire steel structure. The spherical centres of gravity were read from the generated model as X, Y and Z coordinates and made available to the workshop in a special measuring program. The spherical nodes were joined together in a specially manufactured device. The longitude and latitude of the pipe outlets to be set came from the model. Each sphere had a defined south pole and therefore all the necessary angles. Four to five of these nodes were joined together with connecting pipes to form a frame and several frames to form a segment. All distances were measured with a laser. Almost every part of the construction is unique. Without the 3D planning in Tekla Structures, the sophisticated concept of the cloud grove would have been difficult to implement. "We quickly realized that due to the complex geometry, so many connections would come together at one point that we would have no chance of realizing this project with conventional planning methods," explains designer Jürgen Tasch, responsible for the BIM planning of the project. "Without 3D software, it would be conceivable to calculate the whole thing mathematically, but it would no longer be possible to implement it in the workshop."
BIM coordination with the project partners
Using the 3D model, Vollack was able to show the client and architect the complexity of the construction project and explain the concept for implementation in detail. The Tekla Structures model formed the basis for regular construction meetings with the client. The improved visualization of the project using the model is just one of the many advantages of 3D planning. "Change management in particular is much more efficient," explains Jürgen Tasch. "Drawings are generated directly from the 3D model. If the planning changes, the drawings are also updated."
However, the greatest added value of BIM lies in better coordination with the project partners. Vollack used the Tekla Structures model as the central execution planning model for all subsequent trades. Vollack exchanged the model information with the subcontractor responsible for the railing planning via the IFC format. The open exchange format developed by the buildingSMART association is the preferred data format for BIM coordination. 3D DWG data of the spherical nodes was sent to the external production company, which was responsible for the pipe intersections with weld seam preparations. Coordination with the partners for elevator construction, façade construction and membrane construction was also coordinated via the model using STEP and DWG files.
The BIM model in production and on the construction site
In the Wolkenhain project, production in particular benefited from the clear and unambiguous information provided by the BIM model. The team in the workshop was able to access the 3D model of the viewing platform at any time via a laptop in order to get an accurate picture of complex situations and clarify questions. The NC data was transferred directly from the Tekla model to production. Thanks to the 3D planning in Tekla Structures, the steel fabricator was able to significantly reduce the number of drawings. The model replaced additional overview drawings, for example, as item numbers, lengths, weights and material could be read directly from the BIM software.
Vollack was thus able to achieve an extremely high degree of prefabrication and develop a streamlined assembly concept. A large part of the construction could be assembled and welded under protected conditions in the workshop. This also increased planning reliability and saved the team on the construction site a lot of time and nerves. The prefabricated parts were brought to the construction site in 16 segments using special transportation and assembled on site. Concealed screw connections enabled efficient assembly. Welding on site, which is susceptible to the weather, could be avoided. "With 3D planning and BIM, we can build everything so that it only needs to be assembled on site. Every part fits, nothing can be mixed up," explains design engineer Jürgen Tasch. Model-based planning helps the steel fabricator to think about the construction site and the subsequent execution even before the first part is designed. This always pays off afterwards.
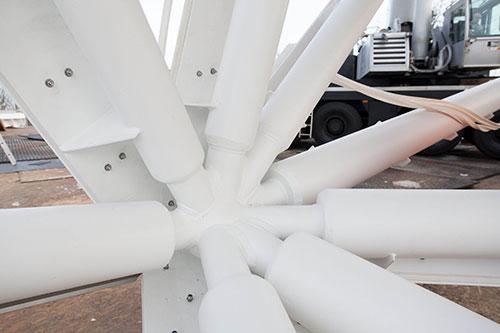
Pioneer in the industry
When it comes to Building Information Modeling, Vollack Hallen- und Stahlbau is one of the pioneers in the industry. Thanks to 3D modeling and BIM, the company can implement challenging projects intelligently and efficiently, offering its customers real added value. In the Wolkenhain project, Vollack met committed partners who also rely on the advantages of model-based planning and execution. However, there is still a long way to go before BIM is used across the board in Germany. Not all companies in the industry are already so open to the topic. Jürgen Tasch still frequently encounters skepticism on the part of project partners. "We are slowly introducing our partners to the project and its structure. People should be convinced and not feel persuaded," explains Tasch. To do this, he first brings the notebook to the construction meeting: He succeeds in illustrating the project where those involved might otherwise be unable to imagine more complex details of the project. Vollack manages to convince by meeting his partners where they are. This begins, for example, by introducing partners who do not work with the model themselves to it via a 3D PDF document. This gives them a better understanding of the project. When Tasch leaves the construction meeting, the initial skepticism usually turns into a request to "bring the laptop and the 3D model next time". The first step towards joint BIM-based planning and coordination has then often been taken.
Added value for the entire building life cycle
The entire project benefits from BIM-based planning and execution. This is especially true if the architect can already provide a model that is as well developed as possible. The more information available to the steel fabricator at the beginning, the more precisely he can design his own, high-performance offer. What looks like more work at the beginning is priceless in the later phases of the project. The increased efficiency as the project progresses benefits all trades.
Vollack is breaking new ground to test modern technologies in combination with BIM - whether in the office or on the construction site. The company has already tested the added value of 3D laser scanning in several projects. The point cloud recorded with the laser scanner can be fed back into the BIM software. This opens up exciting possibilities, particularly for the subsequent maintenance and repair of structures. For example, if wear-related damage occurs to a bridge over the years, a laser scan can be used to quickly record the situation on site. If a 3D model already exists, the scan can easily be compared with the original construction. "This allows us to see directly if something has become deformed, for example, or how a specific support can be replaced," explains Jürgen Tasch. "This opens up completely new possibilities."
Encouraging the industry
BIM-based processes and technologies bring with them many opportunities. With its long digital history, steel construction has great potential to help shape change and reinvent itself. Design engineer Jürgen Tasch therefore wants to encourage the industry to play an active role in the process. "As steel constructors, we have the know-how and the experience. We are responsible for the execution. That's why we shouldn't let the BIM coordination be taken out of our hands, but rather get actively involved," he emphasizes. "Once people have experienced BIM as a new technology and have had a good experience, they are enthusiastic."
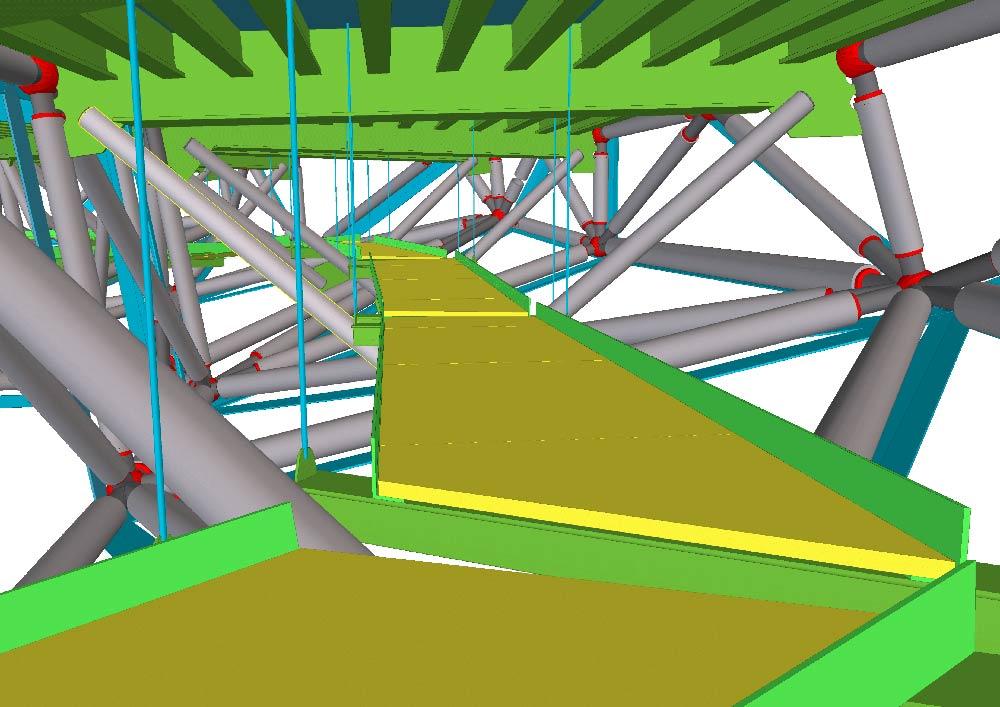
Vollack Hallen- und Stahlbau will continue to lead the way as one of the industry's pioneers and demonstrate the possibilities of BIM in complex projects time and time again.
This article first appeared in metallbau, issue 12/2018.
Image material: Lichtschwärmer; Vollack Hallen- und Stahlbau