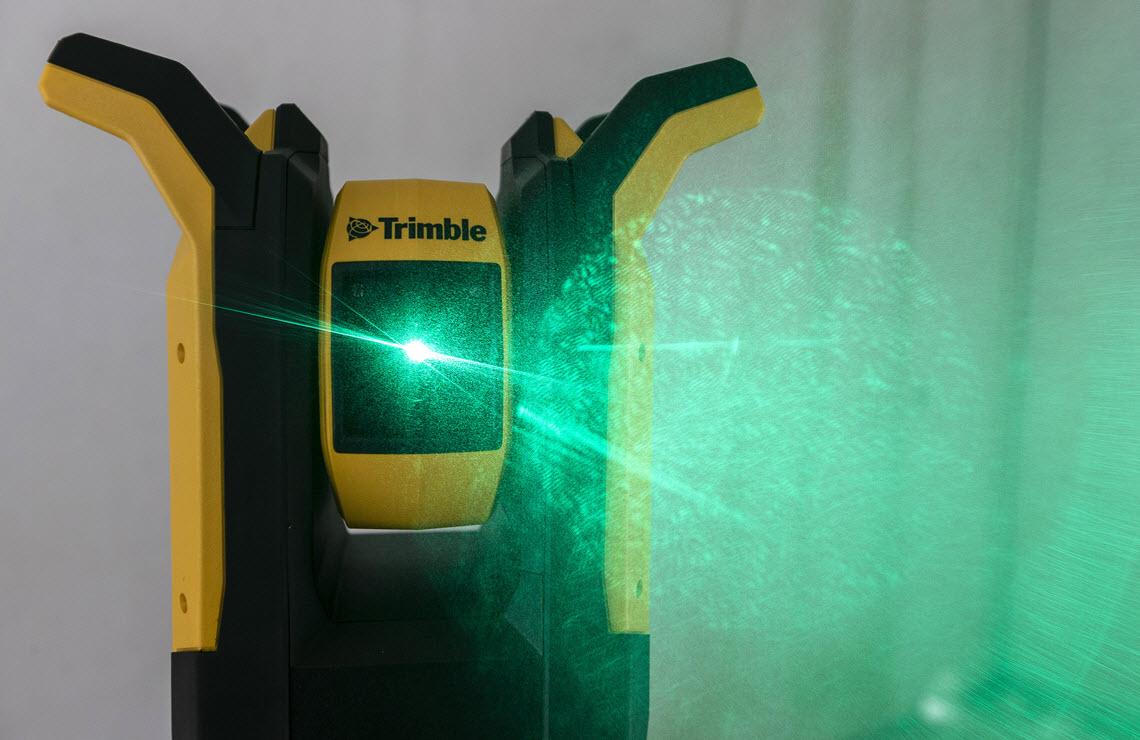
From "Field to BIM" to "BIM to Field"
You may have heard of Field to BIM, the process of capturing digital data with a laser scanner, which is then transferred to CAD software for further processing. Closely related to Field to BIM is BIM to Field. In BIM to Field, the data from the BIM model is transferred to the construction site - in Field to BIM, the data from the construction site is transferred to the model. This is what the Field to BIM - BIM to Field workflow looks like:
BIM workflow "Field to BIM" (above) and "BIM to Field" (below): As-built survey using 3D laser scanning, 3D modeling, as well as planning and staking out for implementation.
Find out more about BIM to Field? Learn in the webinar how you can save time, increase profits and avoid mistakes on the construction site.
BIM to Field: What is it?
Most people are familiar with the term BIM to Field, but what exactly does it mean? BIM to Field (also: BIM2Field) describes the process of transferring digital data into an information model in order to document the exact construction, operation or maintenance on site.
"Capture accurate digital data + use this data to inform accurate work on site"
Robotic tools make it possible to transfer model data to a portable tablet device in the field. This data is then forwarded to the robot, which enables accurate mapping from the information model with the laser measurement system to a tolerance of 2 mm. This technology corrects points on uneven surfaces and localizes wall penetrations. Deviations in the model data due to changing conditions on site can be logged and reported back to the project team as as-built data. In terms of efficiency alone, one person using manual methods can set five times as many points as a two-person team.
And this is how it works:
The stakeout points are marked on the construction plan in the CAD program and exported. The data is then imported into the software that controls the robot. These are displayed as a plan on the measuring/staking device. The devices laser directly onto the ceiling, walls or floors. The points are then marked out, calculations are carried out or individual marking out points are documented with coordinates and photographed, for example in the event of collisions.
Some advantages are:
Saving time on the construction site
Elimination of construction errors by working exactly according to plan
Higher ROI through efficient work and error prevention
Measure and stake out from the CAD plan to the construction site
This approach from the BIM workflow was successfully implemented with the help of the Rapid Positioning System (RPS) surveying device. Kurt Lüscher AG, an electrical installation company from Aarau, was able to significantly speed up the setting out and measuring process in a direct comparison with the measuring tape. During formwork work on a concrete structure in Veltheim, Switzerland, the Rapid Positioning System was able to export plans and stakeout points directly from the CAD program on the construction site. But how exactly does this process work?
The digital data from the CAD program is first transferred to a portable tablet device thanks to the IFC interface. This device is connected to the surveying device, which transfers the digital data in seconds to the robot, which uses its laser measuring system to accurately stake out the information model. Severin Meier, system integrator at Kurt Lüscher AG, has been able to make successful use of this technology: "We are faster, it is easy to insert and, above all, accurate". As it is not only the speed, but also the accuracy and ease of use of the measuring devices that are convincing, this method is completely preferred to the traditional measuring tape.
From tape measure to robot
Digitalization and BIM play an important role in the construction logistics processes of Dutch installation company Megens. Technical Manager Armand van Andel explains: "Our vision is to always proceed in such a way that the next person in the construction logistics process can take over and continue the work without any problems." What has always proved to be a challenge in recent years, however, has been the transfer of the accumulated knowledge to the installer who ultimately carries out the installation. Armand explains: "The information is there, but the big question is: where and how do we share it? We often hear that it takes a long time for the information from the model to arrive directly at the construction site.
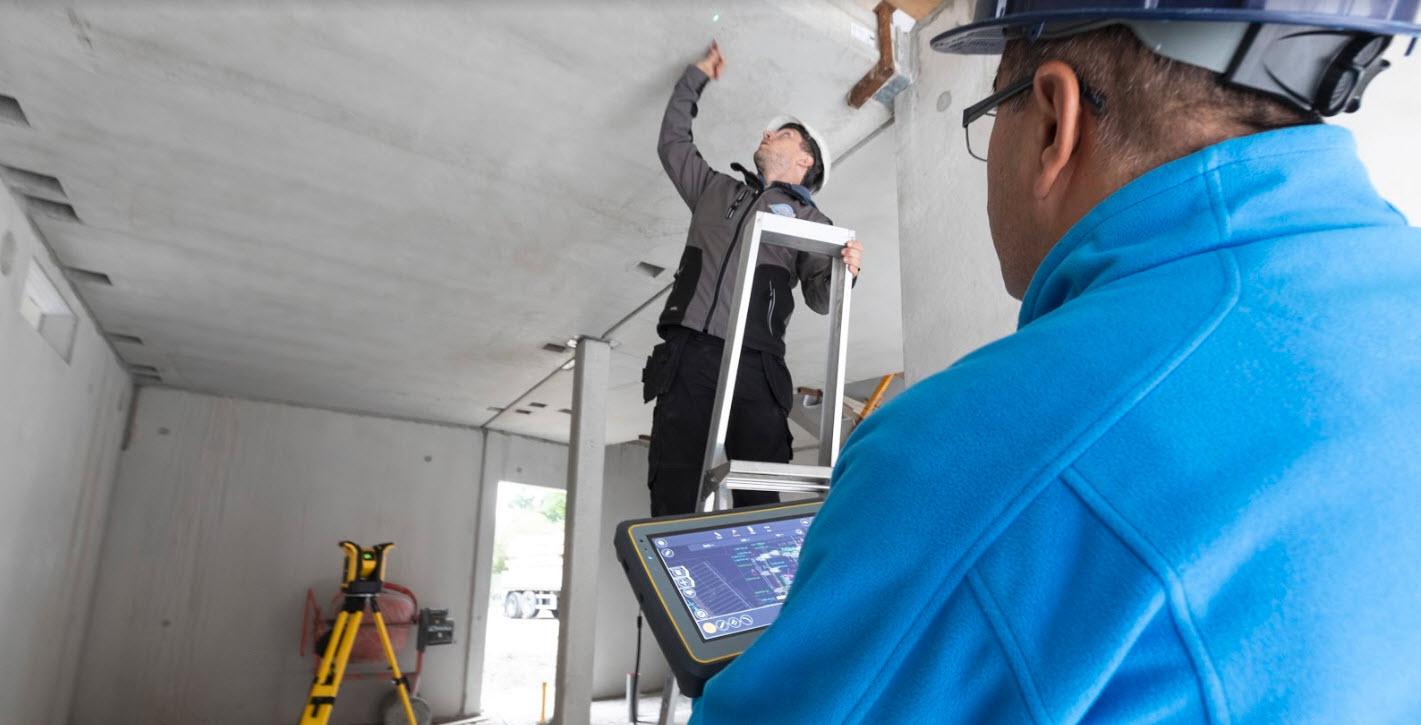
"We only had to move the robot once to create all the points and we were done."
Megens has found the solution in technology: a robot that transfers the information from the BIM model to the construction site. This robot uses a laser beam to indicate the exact positions on the construction site that correspond to the points specified in the BIM model. In this way, the information created in the office is transferred to the construction site quickly and precisely.
"What's more, using the robot brings an even more important advantage: apart from the time you save by speeding up the process, the employees can do what they are supposed to do: Namely, do the installation. If you can increase the time employees spend productively by 10%, that makes a big difference." What's more, you achieve the savings not only on the construction site, but also when creating the model, explains Armand: "The number of hours you spend measuring in the model is significantly reduced." Once the model has been created in our CAD software, the engineer can easily mark points using the Trimble Field Points plugin. These points can be quickly exported for use by the robot, which also saves a lot of time.
Optimal data exchange process
The consequences of inaccuracies in manual execution used to have a major negative impact on the subsequent work process. But thanks to modern technology, three-dimensional digital planning and implementation on the construction site opens up attractive new possibilities. With BIM to Field, the points from the building model are elegantly marked out digitally, paperlessly and quickly directly on the construction site. In this way, the installations of several subcontractors can be precisely positioned at the same time, which ensures that there are no delays on the construction site. This speeds up the data exchange process between model, design, BIM and construction site.
Find out more about BIM to Field? Learn in the webinar how you can save time, increase profits and avoid mistakes on the construction site.