Real expertise and construction competence is not only evident in the actual execution of the project. Efficient defect management and quality assurance tools are also crucial to the successful completion of a construction project.
Nobody likes to admit mistakes. However, dealing with them is particularly important on construction sites. This is because defects can not only affect safety, functionality or fire protection. They also serve as the basis for potential warranty claims.
Effective processes can prevent potential damage or risks and facilitate the acceptance of construction work. In this article, we show you how you can set up a solid defect management system and optimize it using software.
The most important facts in brief
Defect management includes the documentation and rectification of construction defects
Efficient processes facilitate building acceptance and prevent high follow-up costs
Digital processes create transparency and significantly simplify troubleshooting
What is part of defect management?
Effective defect management is of crucial importance in the construction industry. It not only ensures the quality of construction work, but also minimizes potential legal and financial risks. But which components are included?
Recording defects: The first step is to systematically record defects. This includes not only visible or substantial defects, but also hidden defects that may only become apparent over time.
Documentation: Not only should the problems themselves be recorded, but also other relevant information. This includes data such as location, time of discovery and any components or trades affected.
Assessment and prioritization: Not every defect has the same urgency. It is therefore important to evaluate and prioritize them. This makes it possible to focus on the really critical problems first.
Root cause analysis: Decisive for eliminating faults in the long term. Why did the defect occur? Is it due to planning, execution or material problems? Identification helps to rule out similar problems in the future.
Action planning: Based on this analysis, a concrete action plan should be developed. What steps are necessary to rectify the errors and who is responsible for this?
Elimination: Clear communication and cooperation between the various stakeholders are required when implementing the plan.
Documentation of the rectification: The rectification of defects should also be documented. This can be used to prove that the problems have actually been rectified.
Monitoring and control: Management does not end with elimination. Ongoing monitoring and control are also important. This ensures that no new problems arise and that the measures taken are effective.
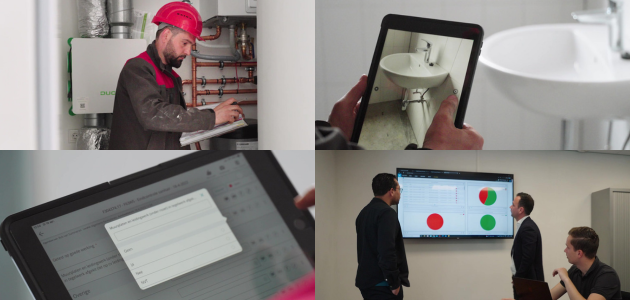
Image: The Dutch full-service installer AGO Technische Installaties relies on the digitalization of work processes in the area of defect management.
What are the legal requirements for defect management?
Dealing with defects on construction sites is not only a question of successful construction project management, but is also based on clear legal regulations. In Germany, two legal bases are essential for this.
German Civil Code (BGB)
The BGB stipulates the requirements in Section 633.2. A work is deemed to be free of defects if it corresponds to the agreed quality.
If no prior agreement on quality has been reached, there are two possible scenarios for acceptable quality. First, the results must be suitable for contractually defined use cases. Alternatively, the quality of the project should be comparable to similar projects in the field.
In addition, Section 631 BGB regulates general contractual provisions for products and services, while Section 650a BGB contains special regulations for construction contracts.
VOB/B (German Construction Contract Procedures - Part B)
It is an essential component of German construction law standards. The standard regulates the contractual relationships between clients and contractors for construction projects in Germany.
This unwieldy title conceals, among other things, detailed regulations for the settlement of defects. Although it is based on the corresponding provisions in the German Civil Code, it is much more specific.
It defines specific requirements for rectification and warranty periods. It also defines the rights of the contracting parties.
Are there deadlines for remedying defects?
The answer to this question depends, among other things, on the type of contract concluded. In Germany, contracts can be concluded on the basis of the German Civil Code (BGB) or the German Construction Contract Procedures (VOB/B) - with different deadlines in each case.
Timely identification and legal enforcement to rectify defects therefore play a decisive role. Both are particularly important in the case of material defects in the construction industry. These become time-barred after five years in accordance with the BGB contract. After that, such complaints can no longer be asserted under the warranty.
Special cases with intent
However, there is an important exception if defects have been fraudulently concealed. In such situations, the law provides for an extended limitation period of ten years.
Construction contracts that are processed in accordance with VOB/B may contain different deadlines. For example, the limitation period for a building is four years, while a two-year period applies to certain parts.
Special deadlines must also be observed in the area of fire protection. Failure to meet deadlines for remedial action in this area can lead to systems being shut down. This can not only have considerable financial consequences, but can also massively jeopardize safety.
What advantages does software offer in defect management?
Defect management is a critical phase in any construction project and digital tools can play a crucial role. The benefits go far beyond replacing pen and paper:
Increased efficiency: Software automates many processes, from recording to defect tracking and rectification. This saves valuable time and significantly minimizes administrative work.
Precise documentation: Software enables comprehensive documentation. Photos, descriptions and time-stamped records help to identify causes and monitor their rectification.
Better communication: The software creates a transparent platform where all parties involved can report and discuss problems. This promotes communication and collaboration, which is crucial for the success of a construction project.
Deadlines: Good defect management software reminds you of deadlines and ensures that defects are rectified in good time. This helps to ensure compliance with contractual provisions and legal requirements.
Data analysis: The collected data can be used to identify trends. This makes it possible to recognize recurring problem areas and take preventative measures.
Mobility: Software such as Viewpoint Field View can also be accessed on the move. This means that faults can be recorded and documented directly on site, which further increases efficiency.
Legal certainty: Careful and well-documented administration can be of great benefit in legal disputes. The software facilitates the provision of evidence and protocols.
Conclusion - defect management in construction projects can be simplified
Complex construction projects with different trades are susceptible to various execution errors. A completely defect-free construction site is therefore more of an ideal than an actual reality.
Dealing with any problems that arise is therefore crucial. Trimble solutions such as Viewpoint for Projects and Field View can create the basis for a transparent error culture and precise documentation.
As a complete construction management software, Viewpoint for Projects is an indispensable companion during all project phases. With the ISO 19650-compliant software in your toolbox, you have control over all aspects of your construction project. The program networks your construction site and provides the precision and overview that digital defect management requires.
Field View translates the overview and control of problem areas and deadlines into concrete construction site practice. The cloud-based tool is the logical evolution of analog recording in the field. Customizable mobile forms for mobile devices finally make pen and paper obsolete - and simplify defect management in the long term.
Find out how AGO Technische Installaties was able to use Viewpoint Field View to its advantage and significantly speed up everyday tasks.