
TRIMBLE TECHNOLOGY SOLUTIONS
Work better with integrated, connected technologies
Optimize your business and end-to-end operations to improve productivity and efficiency. Automate your processes, systemize and empower your data, and connect all people across projects. That's the Trimble difference.
What sets Trimble apart
Technology moves fast. At Trimble, we do more than keep pace. Whether it's applying existing solutions in surprising new ways or opening untapped frontiers to bring the future of technology into today's business, we’re leading the way forward.
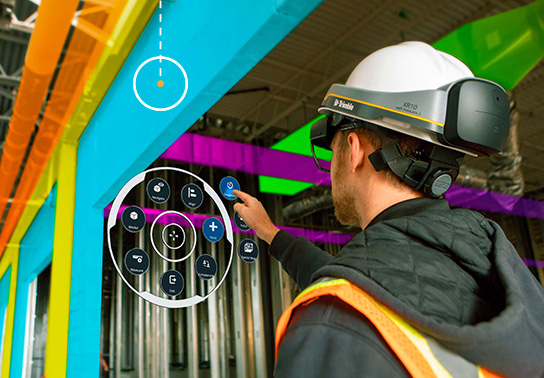
1,000+
unique patents
15%
of revenue reinvested in R&D
25-50%
efficiency gains over traditional solutions
40+
years of industry leadership
125 countries
providing a robust sales and support network
7 million
metric tons of greenhouse gas emissions prevented annually
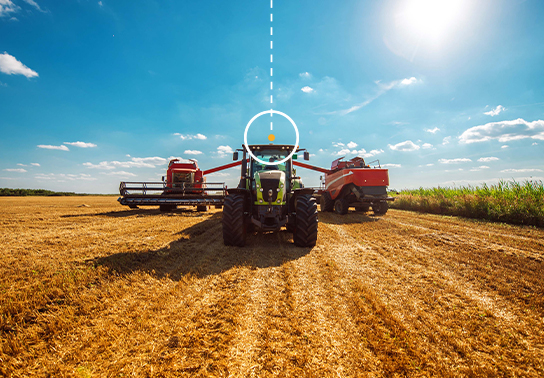
Innovative technology solutions for the industrial ecosystem
Every day millions of people and businesses across many key industries count on Trimble technologies for their life's work.
Analyzing options for net zero energy construction. Bringing safety and speed to urban telecom operations. Syncing data about farm equipment, people and land in one place. While we have hundreds of technology management solutions and innovations changing the way the world works, our core technologies serve as the foundation for how Trimble helps our customers achieve more.

Analytics technology

Autonomy

Connectivity technology

Extended reality

Machine control

Modeling technology

Positioning technology
